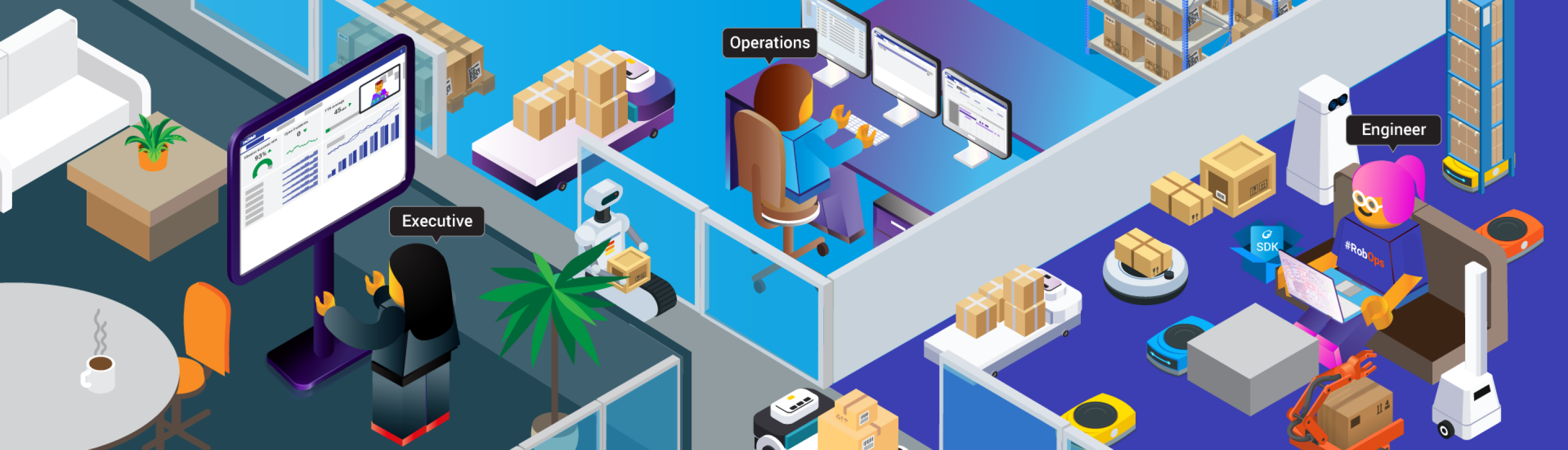

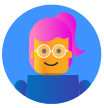

InOrbit optimizes data flow through our unique Adaptive Diagnostics™, which allows us to process massive amounts of data and adjust to the changing conditions on the robot, the network and the cloud. Our platform also manages bi-directional connectivity with the cloud and provides a real-time dashboard with advanced, robotics-specific functionality. Beyond mere monitoring, InOrbit enables notifications, workflows, and remote (manual or automated) interventions such as auditable, secure actions on individual or custom collections of robots.
The goal of most robotics deployments is to efficiently carry out repetitive tasks in a cost-effective manner. This often requires a different set of skills from the research and development origins of most robots. InOrbit leverages our operational expertise to offer the most effective robot fleet operations available. By partnering intimately with service providers and bringing onboard remote operators, InOrbit lets you stop worrying about operations, so you can focus on your unique value proposition.
Complex operations often require coordination between different types of robots, systems and people. Whether this coordination is industry, application-specific, or tackled by domain experts, InOrbit can provide an abstraction layer for common operations across different types of robots, from shared maps and context to mission management and dispatching. Elegantly plan and coordinate your fleet actions harmoniously with their environment.
By integrating cloud intelligence with data on the edge and the robot itself, InOrbit makes it easier for operations and development teams to gain key insights and improve their robot fleet. As a fleet grows, companies necessarily must shift from managing robots individually to automating certain responses based on real-time data and algorithms. For example, multivariate anomaly detection and condition management can achieve far better results than manually-set thresholds on several variables, reducing the common problem of alert fatigue. Make the most of your robots with a platform that allows you to constantly improve.
Scaling a robot fleet requires continuous learning from patterns and edge cases emerging in the field. InOrbit’s agent runs on each robot to optimize data collection, analysis at the edge, and transmission to the cloud for further processing. Leveraging InOrbit’s Adaptive Diagnostics allows the agent to adjust the data sampling rate, resolution and summarization in real time, adapting to specific needs across the fleet.
Effective robot operation demands both real-time intervention and the ability to retrospectively review certain situations to analyze incidents. InOrbit offers a simple, powerful interface to reveal and filter captured incidents (and trends) by any criteria. From there you can dive into the specifics of the situation, with the underlying dynamic data front and center for the duration of each incident. In-app notifications, as well as integrations with collaboration platforms, can help notify the right person on incidents.
Occasionally robots may require more direct remote interventions, whether to relocalize a lost robot, respond to false positives from the computer vision system, or move around physical obstacles. InOrbit offers several levels of teleoperation and controls to enable remote operators to achieve situational awareness and if necessary take over, usually just for a few seconds, to put the robot back on track and get it back to autonomous operation so it can make its way forward in its mission
Autonomous robots are often dispatched to complete specific tasks or missions. In the case of mobile robots, this may involve following paths or moving between predefined locations; cobot arms may be physically interacting or manipulating items around them. InOrbit helps plan these missions, track progress and status, and identify situations where the robot needs extra help to complete its mission.
Robotics developers must learn from failure situations and edge cases to improve the degree of autonomy and reduce the need for remote interventions. However, the tools that work in the lab do not necessarily work for a distributed fleet. Using InOrbit Time Capsule and Data Backfill capabilities, roboticists and software developers can benefit from cloud access to detailed robot data and personalized views that let them drill down to individual robot features, perform easy retroactive analysis, and identify the root cause of a problem.
Observing a robotic fleet is not simple, and every company has its own metrics to indicate the overall health of the fleet. InOrbit’s interactive, real-time dashboard can support any level of observation/control. Featuring high-level key performance indicators, slice-and-dice fleet visualization, and drill-down to individual robots, InOrbit’s configurable widgets let you showcase or explore any metrics. Customers can use extensive yet intuitive settings or APIs to adapt the dashboard to their specific needs.
Modern robots can operate autonomously in semi-structured or unstructured environments; however, there are practical limits to autonomy based on the unpredictable nature of these environments. InOrbit makes cloud-enabled remote interventions possible, whether automated based on configurable triggers or performed manually by an operator. These interventions make it possible to reduce downtime while minimizing operational cost. Through InOrbit’s Actions, companies can execute remote actions securely with a single click, giving operators without technical expertise the ability to effectively handle most situations.
Enabling direct SSH (secure shell) access to robots may be OK in the lab, but exposes robots in the field to unnecessary risks, such as password sharing, cut-and-paste errors for custom commands, etc. Some robotics deployments may rely on VPN (virtual private network) connections to achieve a degree of security, but this often results in connectivity issues.
InOrbit handles end-to-end security for all data communication between its agent and the cloud, establishing a secure, reliable, bi-directional channel with advanced key management. In addition, data is protected on the wire and at rest, using dedicated cryptographic keys.
Leveraging the abundant data from a variety of robot data sources, InOrbit can apply artificial intelligence and machine learning techniques to analyze patterns to generate actionable insights and recommendations that translate into cost savings through efficiencies. This can help companies anticipate problems before they occur.
In order for robots to continuously improve their efficiency, their software must evolve in response to new data. New software versions must be matched to specific hardware. In addition to its core algorithms, each individual robot may require specific information to operate in a given environment, such as maps or schedules, which may change frequently. As part of advancing the state of the art in RobOps, InOrbit enables configuration management best practices, allowing companies to remotely update the configuration and software on the robot over the air, either individually or through configurable collections.